Automotive DMS for OEMs and Dealerships
The Most Powerful Vehicle Management System
Industry’s most intelligent and data-driven Dealership Network Management System, built for automotive retailers. It combines modern technology, scalable architecture, and customer-focused automation with advanced analytics and AI-powered insights to drive meaningful growth.
Streamline operations, boost efficiency, and deliver exceptional customer experiences across your entire dealership channel network with our AI-powered DMS platform built specifically for dealer and service network, Electric Vehicles segment, and heavy equipment, EV segment and heavy industrial machinery sellers.
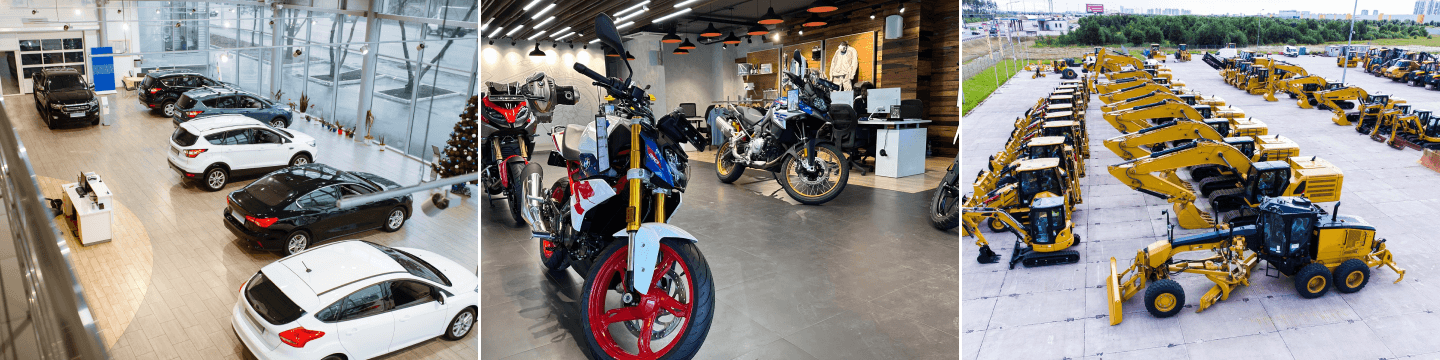
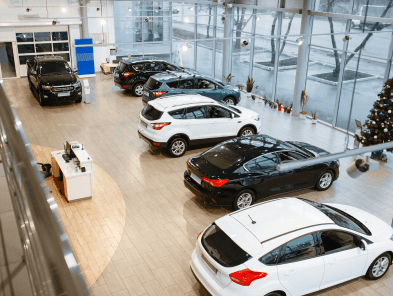
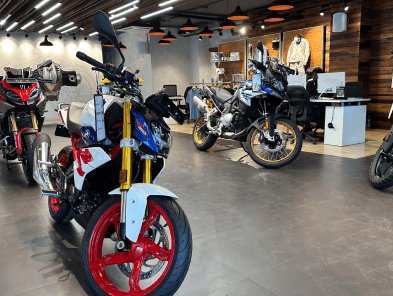
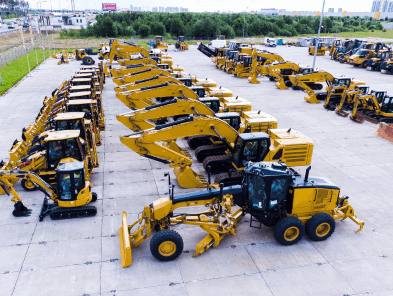
Automotive Dealer Management for OEMs and Dealerships
Elevate your dealerships performance with Intelligent automation, AI-driven insights, streamlined operations, and exceptional customer experiences.
Excellon Automotive DMS reimagines how OEMs and dealerships manage their operations, integrating sales, service, inventory, and customer engagement into a seamless, agile platform. Our DMS empowers you to take sales and after-sales strategies to the next level.
By leveraging AI-driven insights, we simplify complexities and enhance growth throughout the distribution ecosystem, helping dealerships and OEMs thrive in an evolving market.
200 Million+
10,000+
98%
25 Million+
Vehicles sold through Excellon platform
40%
100%
Vice President, Sales & Customer Care
Mahindra 2-Wheelers Limited
Vice President, Sales & Customer Care Mahindra 2-Wheelers Limited
All-in-one DMS for the automotive and industrial sectors
Sales Management with CRM
Transform your sales operations with our AI-powered CRM that streamlines lead management, automates follow-ups, and provides predictive insights for higher conversion rates. Our integrated solution ensures seamless collaboration between sales teams and delivers personalized customer experiences at scale.
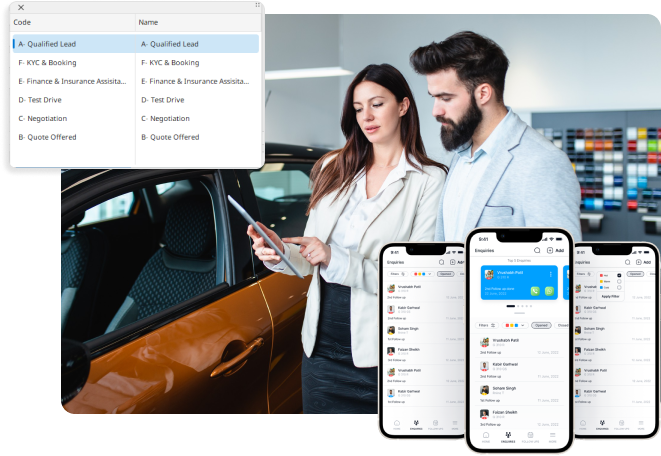

End-to-end sales cycle management

Leads and campaigns management

Lead to quote

Predictive demand forecasting and planning

Integrated call center

AI-driven test drives to bookings conversions

Intuitive mobile app for sales
Empower your salesforce with an intuitive mobile app that provides real-time data, customer information, and sales tools on the go.

AI-powered recommendations
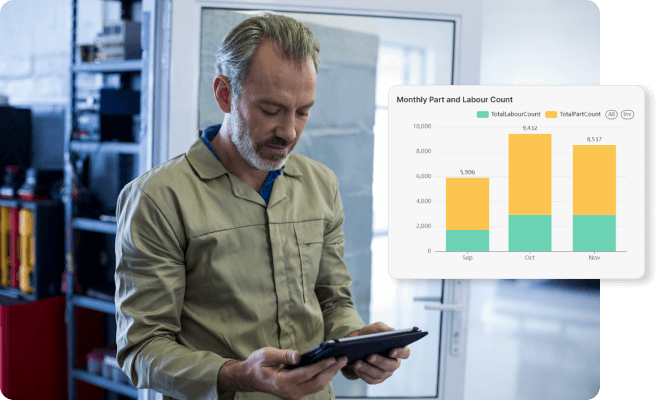
Comprehensive service and workshops management
Ensure your service department delivers an exceptional experience by providing real-time scheduling, job order creation, and AI-powered service efficiency recommendations. Our service management module ensures minimal downtime and maximizes customer satisfaction.
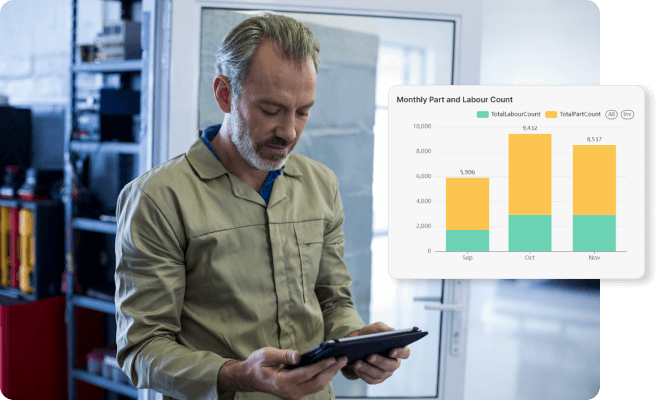

Service appointments scheduling

AI-powered repair job order creation

Estimates, claims and warranty management

Automated service bay and technician allocations

Automated customer reminders and communications

Integrated technician mobile app

AI-powered recommendations for service efficiency
Empower your salesforce with an intuitive mobile app that provides real-time data, customer information, and sales tools on the go.
Smart inventory and spare parts management
Keep your inventory lean and responsive with real-time tracking, AI-driven replenishment, and integrated parts warehouse management. Optimize your stock to ensure you have the right parts and vehicles at the right time, avoiding overstocking or shortages.
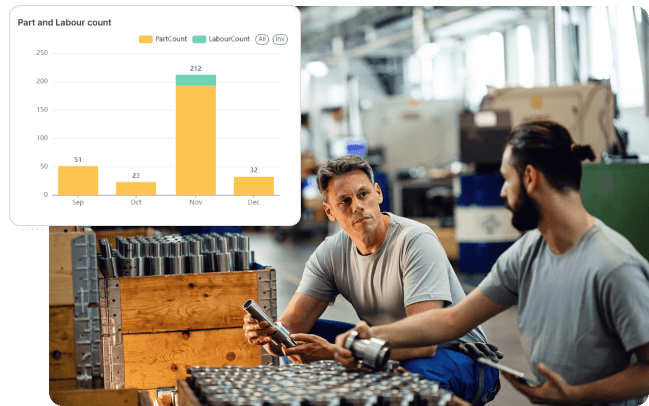

Vehicle inventory management

AI-powered vehicle planning and ordering

Spare parts warehouse management

Parts purchase planning and auto ordering

Stock classification, adjustment and valuation

AI-driven intelligent parts ordering

Inventory movement and trending analysis
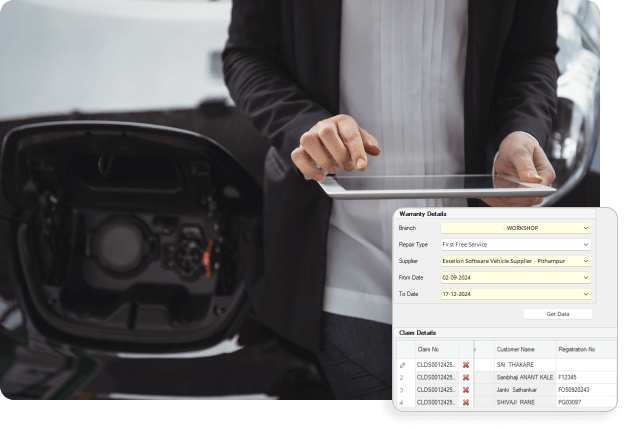
Efficient warranty and claims
Streamline your warranty and claims processes with an integrated solution that ensures quick processing, transparency, and customer satisfaction. Our AI-powered warranty management system reduces manual effort and ensures claims are processed accurately.
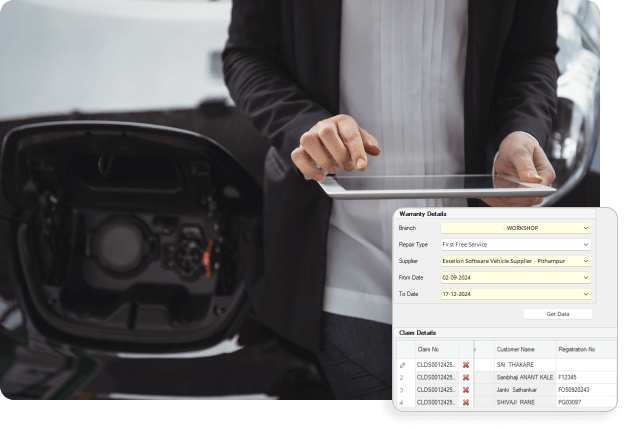

Centralized warranty management

Warranty claim process automation

Claims validations and approvals

Across dealerships warranty claims insights

AI-driven warranty claims analysis

Warranty parts ordering and returns

AI-powered recommendations for service efficiency
Agile pricing and promotions
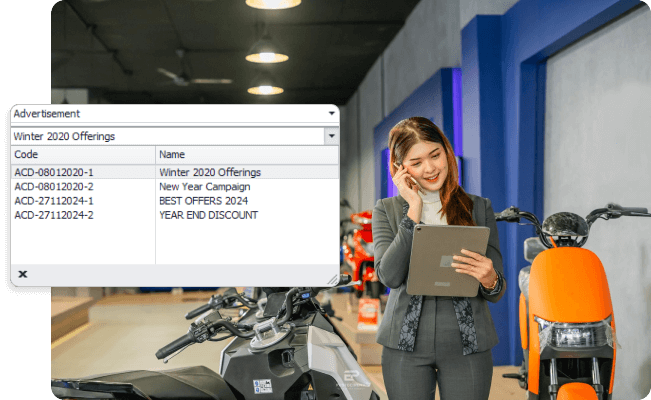

Centralized pricing management

National and regional promotions management

Dealer-specific promotions and incentives

Dynamic pricing algorithms with real-time price adjustments

Targeted promotions and offers

Market trends, demand and price sensitivity insights

AI-powered pricing and promotion recommendations
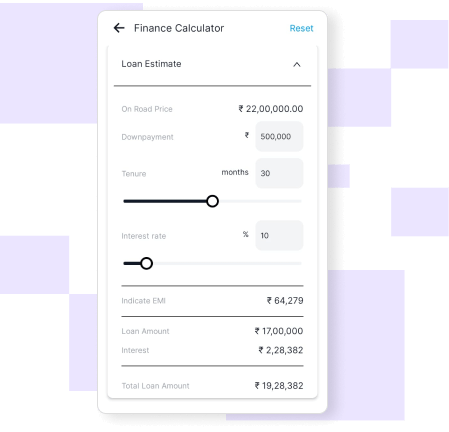
Finance and accounting management
Optimize financial operations and ensure compliance with a fully integrated finance and accounting solution. Our finance module simplifies processes such as invoicing, payments, and cash flow management while providing real-time financial insights.
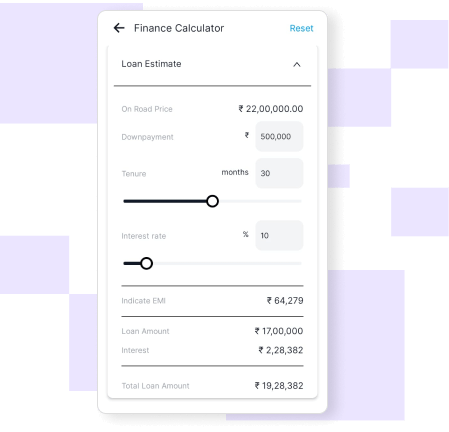

Budgeting and financial planning

Sales and revenue management

Digital invoicing and payments processing

Cashflow management
Get insights into warranty claims across your entire dealership network to identify trends and issues.

Reconciliation and banking

Accounts receivables and payables

Dealership financials
Get a complete overview of your dealership’s financial status in real-time.

Audit and compliance
Ensure compliance with financial regulations using built-in audit tools.

AI-powered financial health analysis and recommendations
Use AI to assess financial health and receive actionable recommendations.
Growth-centric analytics and insights
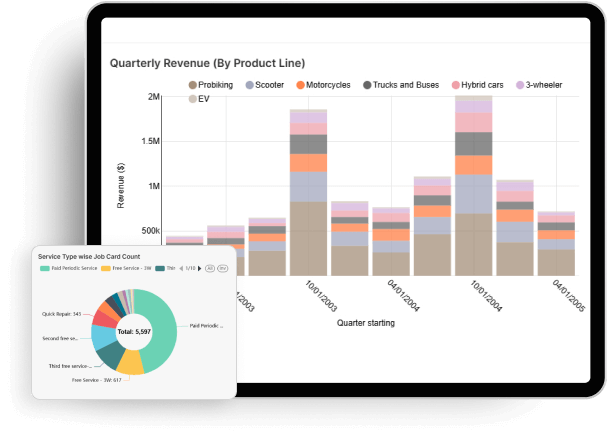

Real-time in-platform 360-degree insights

ETBR reporting and insights

Intuitive dashboards and reports

PerformancePulse

SalesPulse

ServicePulse

FinancePulse
Track financial health and cash flow to keep your dealership profitable by closely monitoring revenue, expenses, and profit margins, ensuring that your financial operations remain sound and sustainable.

OperationsPulse
Get insights into operational efficiency, helping identify areas for improvement, streamline processes, and ensure that dealership’s day-to-day activities are optimized for maximum productivity and profitability.

AI-driven predictions and recommendations
Leverage our powerful ExcellonPulse AI engine to predict future trends, such as sales performance, customer preferences, and service demands, while receiving actionable recommendations that help your dealership take proactive steps towards sustainable growth and enhanced customer satisfaction.
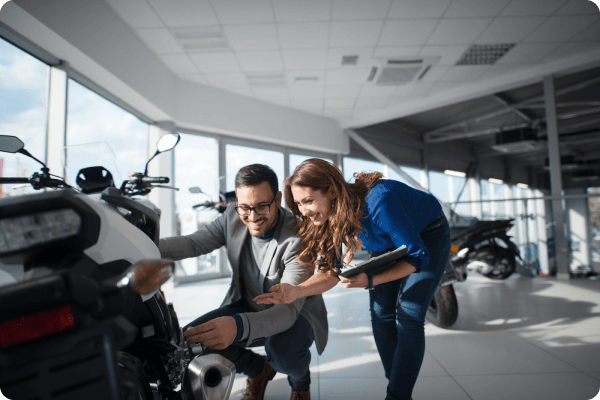
Customer delight
Create delightful customer experiences at every interaction point, from initial inquiry to post-purchase. Our customer-centric tools ensure that customers are engaged and satisfied at every stage of their journey.
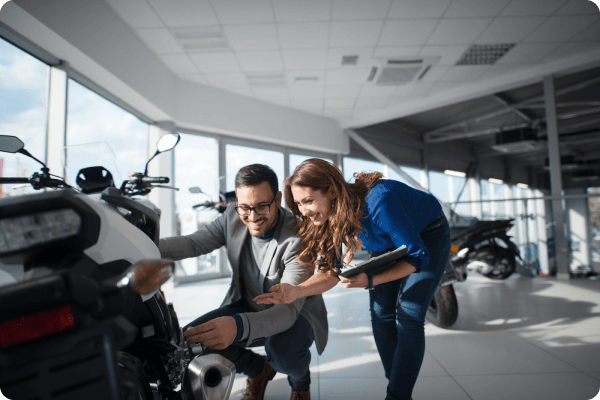

Lead to sales and post-sales customer relationships management

Customer self-service portals

Virtual showrooms and digital experiences

Post-purchase engagement & loyalty programs

AI-driven personalisation

Accounts receivables and payables

High-touch customer engagement and communications

Sentiment analysis and engagement recommendations
Seamless Integration
Excellon DMS delivers seamless integration across your entire automotive retail ecosystem, creating a unified digital backbone that connects OEMs, dealerships, and customers. Our platform’s native integration capabilities enable real-time synchronization with OEM central systems for vehicle allocation, parts catalogs, and warranty processing, while simultaneously connecting your dealership’s core operations – from sales and service to parts and finance.
This comprehensive integration eliminates data silos, automates cross-system workflows, and ensures consistent information flow across manufacturer portals, dealer management tools, diagnostic systems, financial platforms, and customer touchpoints, ultimately driving operational efficiency and delivering superior customer experiences.